Сегодня доля российских компаний в мировом производстве композитов составляет около 1%, а сама отрасль является крайне импортозависимой.
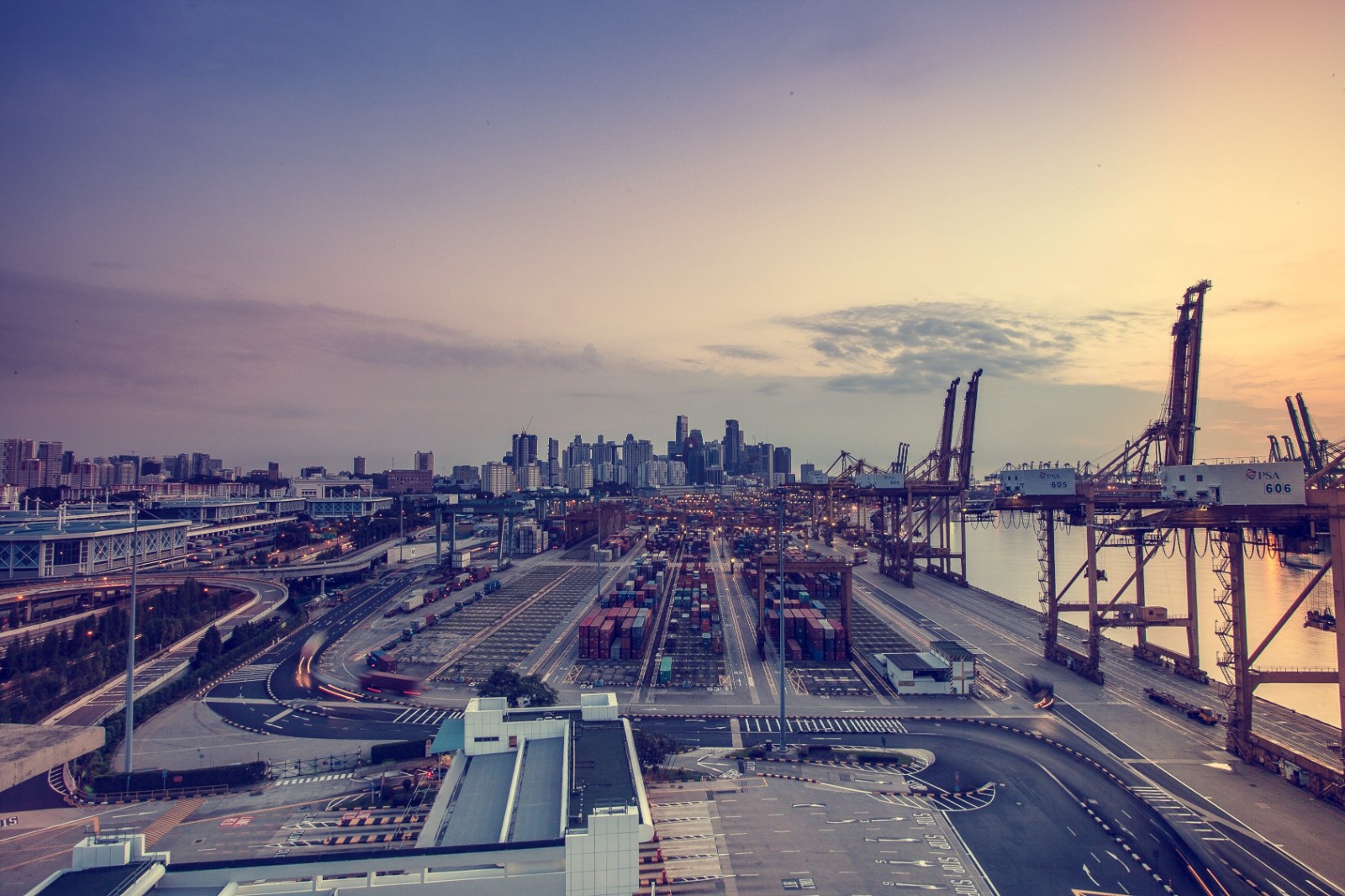
Сегодня доля российских компаний в мировом производстве композитов составляет около 1%, а сама отрасль является крайне импортозависимой. Подпрограмма по развитию производства традиционных и новых материалов, к которым относятся и композитные материалы, включена в госпрограмму развития промышленности РФ. А утвержденная Минпромторгом «дорожная карта» предполагает объемы финансирования за счет федерального бюджета в размере 30517110,7 тыс. рублей. Одним из целевых показателей этой программы является увеличение объема производства в композитной отрасли до 81,3 млрд. рублей к 2024 году.
По данным Минпромторга, производством композитов в России сегодня занимаются более двух сотен предприятий и компаний. В 2018 году по инициативе UMATEX (дивизион «Перспективные материалы и технологии» Госкорпорации «Росатом») на территории Республики Татарстан, Московской и Саратовской областей был сформирован межрегиональный промышленный кластер «Композиты без границ». Участниками кластера являются ведущие промышленные предприятия композитной отрасли и научные организации.
Сегодня UMATEX является лидером на российском рынке в области производства углеродных композитов и входит в десятку мировых лидеров по производству углеродного волокна широкого сортамента. По сравнению с обычными конструкционными материалами (алюминием или сталью) композиционные материалы на основе углеродных волокон обладают экстремально высокими характеристиками: прочностью, сопротивлением усталости, модулем упругости, химической и коррозионной стойкостью, в несколько раз превышающими аналогичные показатели стали, при существенно меньшей массе.
Возможности роста российского рынка углеволокна оцениваются на уровне 3 тыс. тонн к 2025 году, при том, что на сегодня потребление в России составляет в десять раз меньше.
В то же время развитие отрасли ограничивают нехватка квалифицированных кадров и слабое развитие нормативной базы. Процесс сертификации нового материала для возможности его использования в промышленном оборудовании сейчас занимает до трех лет, поэтому очень важно коренным образом изменить порядок разработки новых стандартов и сделать его более компактным и быстрым.
Экономический эффект использования композитных материалов в промышленности
Композиционные материалы превосходят по многим параметрам традиционные металлические. Традиционным материалам с однородной структурой присуще наличие микроповреждений. Для того, чтобы максимально избавиться от них, такие материалы используют в виде тонких волокон: чем тоньше волокно, тем меньше дефектов в его сечении. Такие свойства волокна позволяют достичь более высоких показателей прочности и жесткости. Композитные материалы менее чувствительны к концентраторам напряжений, а низкая скорость распространения в них усталостных трещин обеспечивает повышенную долговечность конструкций из этих материалов.
Главное достоинство любого композита — это возможность при проектировании самостоятельно выбрать тип материала, ориентацию и объемное содержание волокон. Это позволяет получать конструкционные материалы с желаемыми для конструктора функциональными свойствами и делает использование композиционных материалов очень ценным и перспективным направлением в самых разных отраслях промышленности: авиа- и двигателестроении, машиностроении, энергетике, нефтегазовой и строительной.
В любых областях промышленности одной из основных задач является снижение себестоимости производства без потери качества изделий и снижение расходов при последующей эксплуатации изделия. Так применение полимеров и композитных материалов в современном автомобиле позволяет снизить его массу на 15–30%, а снижение массы на 100 кг приводит к снижению расхода топлива на 0,5 и более литров на каждые 100 км. Безусловно, высокотехнологичные композитные материалы не экономичнее стали или алюминиевого сплава, однако им не требуется защита от коррозии.
Известно, что использование полимерных композиционных материалов (КМ) при производстве авиационной и космической техники позволяет снизить от 5 до 50% вес (массу) летательного аппарата (ЛА). Мировые лидеры самолетостроения — корпорации Airbus и Boeing активно применяют в конструкциях своих ЛА композиты. Если в самолетах типа А-340 и В-777 в 2000 году было использовано около 10% КМ от веса лайнера, то в 2015 году эта цифра составила не менее 50%. Общая доля композитов в конструкции МС-21 составляет по разным оценкам 30–40%.
Перспективные отрасли
Области использования композиционных материалов практически ничем не ограничены. И сегодня КМ нашли применение во многих отраслях промышленности.
В машиностроении композитные материалы применяются для создания твердых покрытий на режущем инструменте и защитных износостойких покрытий на металлических поверхностях с интенсивным трением. Из углепластиков в сочетании с алюминиевой сотовой конструкцией изготавливаются ответственные детали и узлы космических ЛА, подвергающихся интенсивному нагреву и большим перегрузкам. В военной технике КМ применяются при изготовлении бронежилетов и защиты танков и вертолетов от пулевого и осколочного поражения. В горнодобывающей промышленности — при изготовлении резцов для бурения скальных пород, а в перерабатывающей промышленности из КМ и полимеров выполняется облицовка измельчителей для размола твердых веществ; в турбостроении — для создания лопаток; в химической промышленности — для автоклавов и цистерн для хранения и перевозки химических и нефтепродуктов.
Трудности разработки композитных материалов и способы решения
Разработка и создание деталей из композиционных материалов, а также разработка и исследование характеристик нового материала являются комплексом сложных и связанных задач. Подход к решению таких задач заключается в выборе оптимального сочетания технологий и материалов; проведении компьютерного моделирования напряженно-деформированного состояния конструкции и технологических процессов производства; организации экспериментальных исследований для определения исходных характеристик материалов. Одна из ведущих российских авиастроительных компаний недавно столкнулась с трудностями при попытке перед изготовлением точно смоделировать рабочие характеристики деталей композитной конструкции. Их трудности были связаны с более сложной природой нового материала, из-за чего в результате у них случился неожиданный отказ.
Способность точно предсказывать поведение композитных материалов во время производства, а также прогнозировать свойства уже готового изделия имеет решающее значение для обеспечения уверенности в конструкции, поддержки изначально правильного подхода, увеличения доли использования композитов и ускорения их внедрения.
Задача точного моделирования композитного материала заключается в получении точного описания его состава. В отличие от обычного материала (например, стали), композит, как правило, представляет собой смесь волокнистых материалов различной толщины, которые могут быть наслоены друг на друга для создания единого материала. Ориентация волокон в каждом слое (направление основного волокна) отличается с точки зрения угла расположения, толщины и материала, расположенного слоем выше и ниже. Эта сложность компенсируется гибкостью, позволяющей локально настраивать свойства жесткости и прочности в каждой детали.
Инженерные проблемы конструкций из композитных материалов могут быть решены только с помощью детального анализа методом конечных элементов (МКЭ) и узкоспециализированных инструментов моделирования. Сегодня на рынке есть несколько систем для компьютерного моделирования изделий из композитных материалов и виртуального исследования характеристик КМ. Среди них программное обеспечение компании Ansys. Программный модуль Ansys Composite PrepPost позволяет создавать модели конструкций из композиционных материалов и обмениваться данными с другими программными продуктами Ansys. Для анализов результатов решения в модуле Composite PrepPost реализована возможность комплексной оценки модели по нескольким критериям разрушения (подробнее о программном модуле Ansys читайте в новом номере журнала «Композитный мир»).
При работе с композитами исследование отказов также отличается от исследования отказов при работе с обычными материалами. В совокупности инженеры анализируют локальные сбои, чтобы определить, где, как и при каких условиях нагрузки происходит сбой. Композиты могут выходить из строя разными способами (расслаивание, разрушение матрицы, повреждение волокна при сжатии или растяжении). Оценка сложных режимов отказов является ключевой задачей при проектировании композитных конструкций.
Ещё одна проблема — взрывной рост количества и усложнение данных о перспективных материалах. Достаточно сложно определить и выбрать жизнеспособные материалы и варианты обработки из быстро растущего набора возможностей. Это требует наличия хорошей базы данных, отражающей весь спектр этих возможностей и предоставляющей инструменты для поиска нужных данных.
Ansys уникален тем, что помимо многодисциплинарных инструментов для моделирования композитных материалов, он также предлагает набор инструментов для сбора и хранения всей информации о корпоративных материалах — Ansys GRANTA MI. Этот набор инструментов основан на лучшей в отрасли базе данных о материалах и решениях для управления данными о материалах, и охватывает весь жизненный цикл продукта от концептуального проектирования до производства композитов и производства изделий из композиционных материалов и металлов.
С учетом всех трудностей, с которыми сталкиваются инженеры и конструкторы при разработке изделий на основе композитов, создание ИНТЦ является своевременной и актуальной задачей.
compositeworld.ru